Our PCB Shop
The in-house process from electronic components to musical masterpieces.
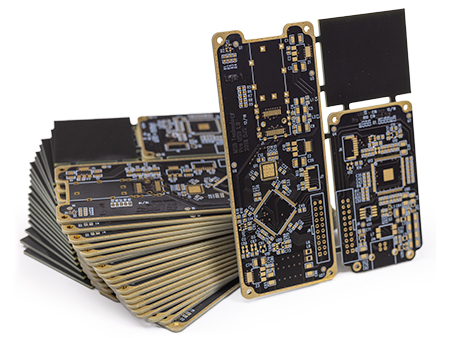
Step 1 – American Made Circuit Boards
Each of our circuits begin its life in the heart of California’s Silicon Valley. By locally sourcing each circuit board we produce, we maintain tight control over our circuit board quality. Every custom board is produced to our exacting standards, and is extensively tested and inspected before being delivered to us for assembly. Our supplier has over 45 years of circuit board manufacturing experience and produces only the most reliable circuit boards available.
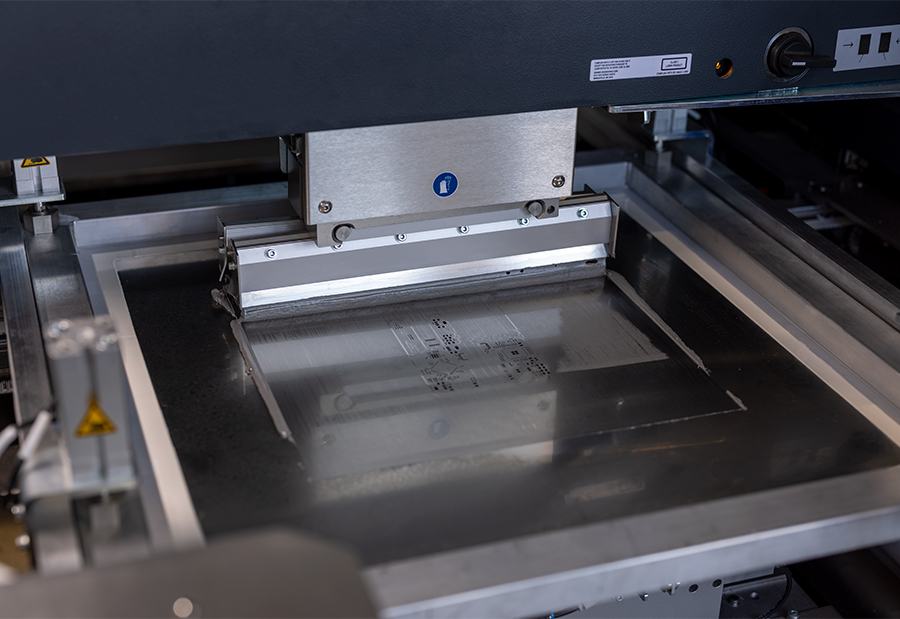
Step 2 – Solder Paste Printing
Because each electronic component must be attached to the circuit board with a small amount of molten metal, we start with solder paste: a paint-like mixture of tiny beads of solid solder alloy mixed with stabilizers and fluxes. But humidity and temperature fluctuations can rapidly deteriorate this mixture; to combat these effects, our printing machine has complete interior environmental control to keep the solder paste in an optimal state during production. The solder paste is then accurately screened through a laser-cut and polished stainless steel mask. The paste precisely covers each of the thousands of gold plated copper pads, where the component leads will be soldered. Each board is accurately positioned, lifted and screened with the solder paste to an accuracy of +/-0.001” (+/-25 µm). Then our unique printing machine performs a 3D LIDAR scan of the entire board to measure the solder paste coverage, volume and height of every printed pad. Any problems are flagged and defective prints are rejected, cleaned, and sent through the printing process again. The perfect structure of solder paste print guarantees perfect soldering later in the assembly process.
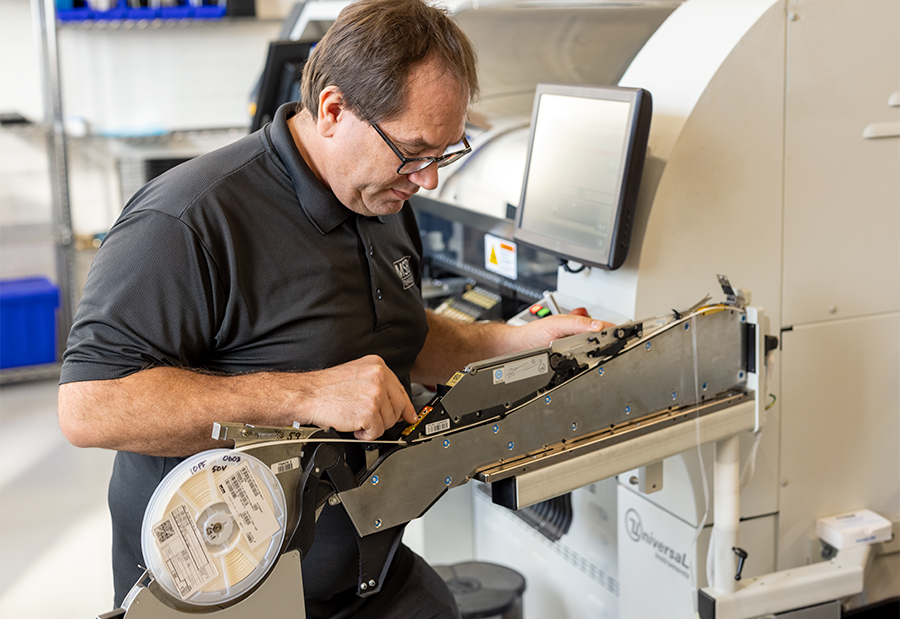
Step 3 – Part Assembly
A circuit board is useless without its electronic components. In the next step of in-house production, a dedicated high-speed assembly robot installs the components by carefully pressing each one into the solder paste. This temporarily glues it into position until it can be soldered. Each part is picked from its packaging (paper or plastic strips with cavities, plastic tubes or trays) seven at a time using precisely designed vacuum nozzles. Each part is then photographed by a high resolution camera while high-speed optical recognition software measures its precise location and orientation. From there, the machine carries the part to its home over the circuit board and places it gently into position. Just one of our custom designed circuits can have as many as 4,192 individual components per board, so we require a speedy assembly machine. Our machine can select, inspect and place parts at the rate of 15,300 parts per hour–four parts every second.
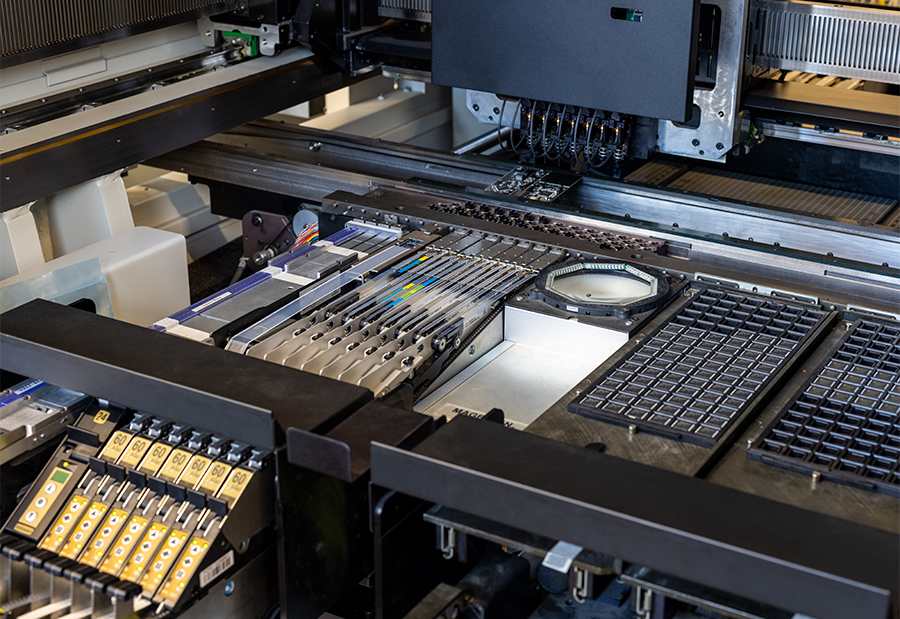
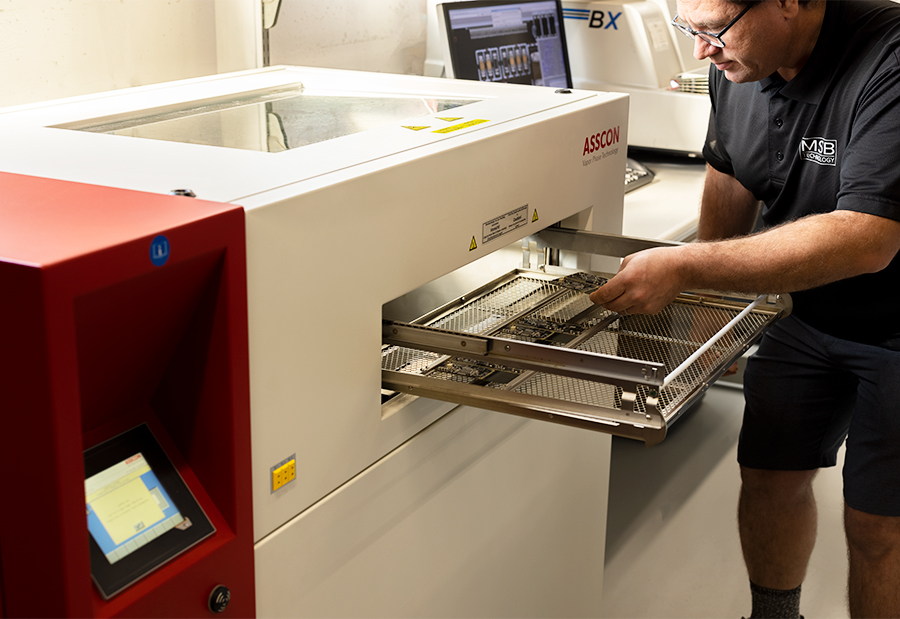
Step 4 – Reflow Soldering
The components now require a permanent bond with the circuit board. To achieve this, the entire board is slowly heated to dry the solder paste, chemically clean the tiny solder balls within the paste and then melt it into a molten blob. The board is quickly cooled to solidify the metallic bond between the parts and the circuit board. This is the most critical and stress inducing moment of the entire process. Non-uniform heating, or too high a temperature, can cause parts to drift out of specification–or even be damaged. In other instances, oxygen can quickly attack the surface of the tiny solder balls, oxidizing the solder and polluting its composition.
To combat these issues, we use a unique reflow soldering oven. The circuit boards are slowly lowered into a tank containing a very dense, hot gaseous polymer vapor. The vapor condenses across the surface of the parts to evenly heat them and eliminate any oxygen from the board surface. As a result, each component is evenly heated to eliminate damage by thermal stress while preventing oxidation of the solder. Overheating of the parts is completely prevented, because the parts cannot be heated to a higher temperature than the vapor. This guarantees the highest performance soldering of any available process. It’s also environmentally friendly; we don’t use any toxic chemicals, and we reduce energy use compared to traditional methods.
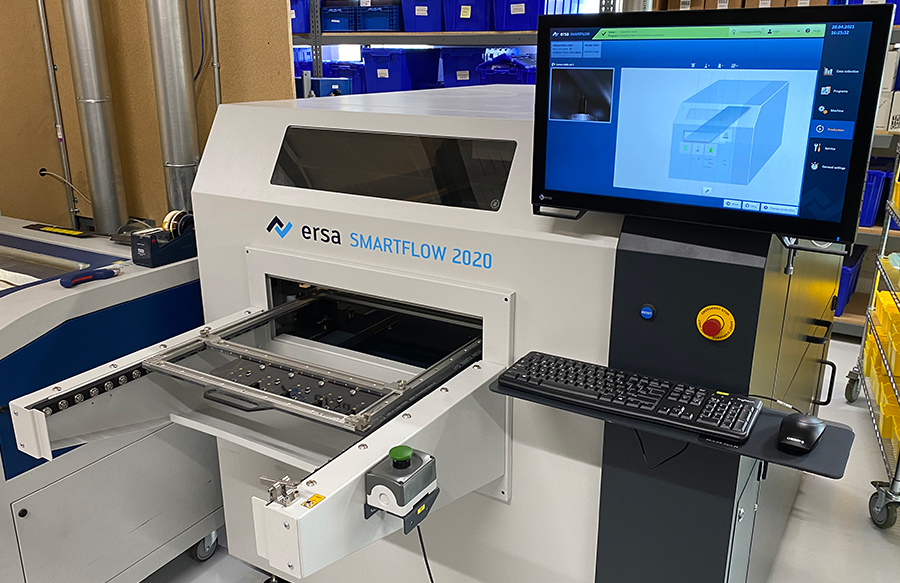
Step 5 – Selective Soldering
The remaining large and bulky components with leads that go through the circuit board (known as through-hole components) are now added by hand. Once prepared, they will processed by our selective soldering machine. This allows us to control the stressful additional heating cycle present in an alternative process: wave soldering. Wave soldering requires the entire circuit board be slid over a molten wave of solder, stressing the smaller surface-mounted components. Selective soldering of the larger components assures the optimal lifetime of every component on our circuit boards.
Step 6 – Inspection
Once the boards are fully assembled, they are all inspected using our AOI or “Automated Optical Inspection” machine. This is required to maintain the high reliability we’re known for with every circuit board we produce. Each part and solder joint is inspected by our AOI machine; any component that doesn’t meet our exacting standards is flagged for rework and human verification. Our machine uses precise 3D scanning to detect each detail of every circuit assembly.
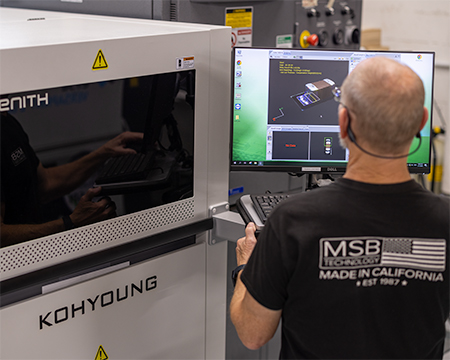
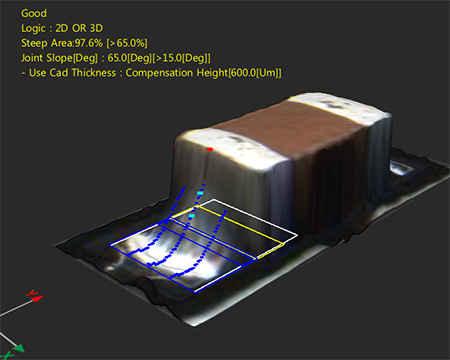
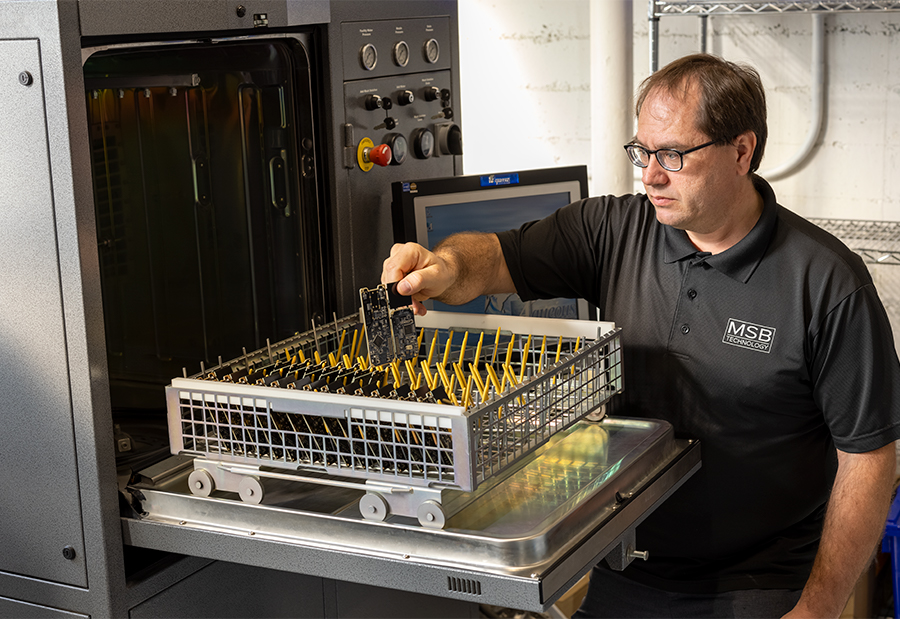
Step 7 – Washing
In order for a circuit board to last a lifetime, circuit corrosion must be minimized. While competitors use a “no clean” flux, it’s anything but clean: remaining residue left on the board surface will very slowly react with the metals of the solder joints. To prevent this, we use a water based flux that is washed completely from the solder joints, ensuring the longest possible lifespan of the circuit boards. Boards are loaded into a batch washer that uses ultra pure deionized water and powerful sprayers to clean any trace of the flux or contamination from the circuit board. Our washer is as environmentally friendly as possible, filtering and recycling its cleaning water in a closed loop.
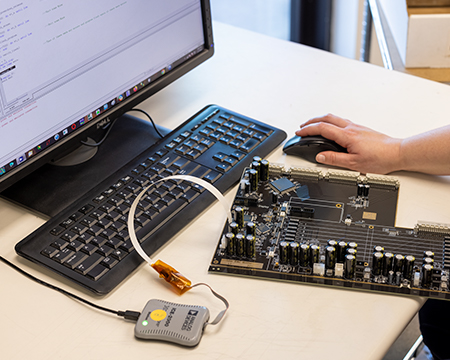
Step 8 – Programming
Modern circuits would be lifeless ballasts without firmware and software to configure and run them. Software programming is directly correlated to the product’s overall performance and utility. We write all of our firmware and software in-house so that it’s tightly integrated with the hardware. Some products have as many as five chips with custom-written software or firmware packages programmed into them before they are ready for installation into an MSB product, guaranteeing our products are as smart as they are powerful.