Our Machine Shop
The in-house process that transforms raw metal into the stunning product you know and love.
Step 1 – Industrial Design
The chassis design has a critical effect on the product performance and manufacturing workflow. Once layout, aesthetics, isolation, and cooling are optimized, we carefully program our CNC (Computer Numerically Controlled) machines to carve massive blocks of raw aluminium into their final shapes. Each unibody chassis may require up to eight hours of autonomous machining to produce the intricate and fine details that set our products apart. The production process is fine tuned; whether it’s the product design or careful selection of our cutting tools, everything works in tandem to obtain the finest surface finish on each part.
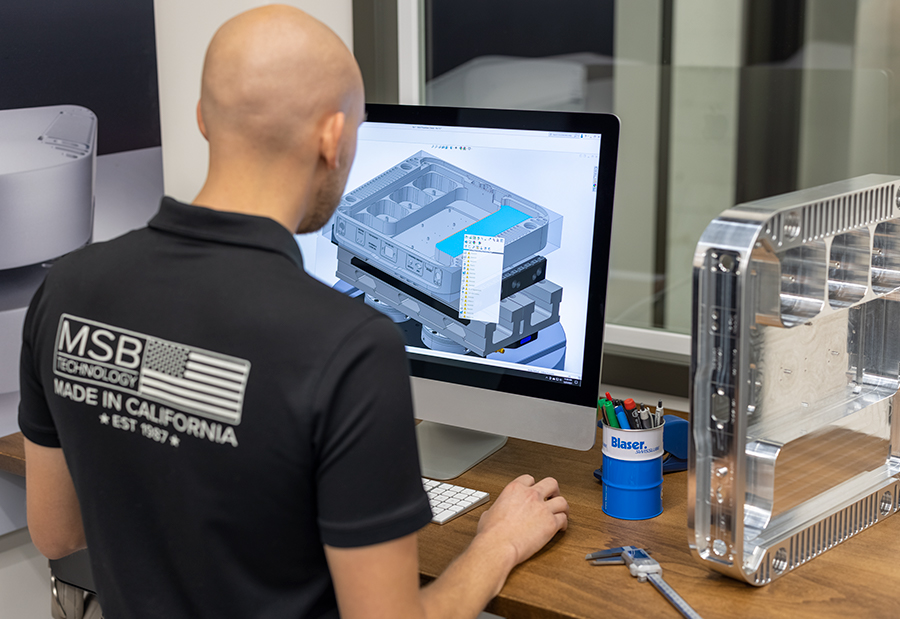
Step 2 – CNC Programming
Our milling machines wouldn’t be what they are without the code to run them. With the help of cutting edge CAM software (Computer Aided Manufacturing) we individually write the cutting paths that carve each metallic billet into its final form. Even though the automatic tooling and profile selection of our CAM software are advanced, it still can’t beat the human intuition and instinct our team possesses. We carefully evaluate the accuracy and finish quality of every cut. While working on a prototype, we’re able to go from a design concept to a finished part in a day. This process is always improving, resulting in more efficient manufacturing and more feature-rich designs.
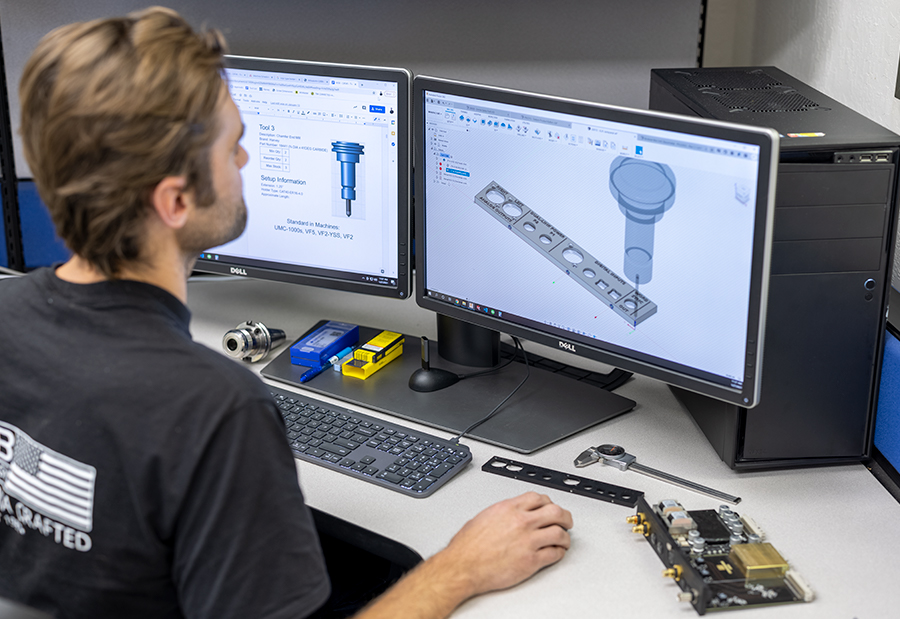
Step 3 – American Made Metals
During the last three decades, we’ve built strong relationships with top quality suppliers who ensure we get the best North American-sourced metals for our machine shop. For example, we pay a premium for the top-tier Kaiser “Select” aluminum plate, a leader in anodizing quality and performance. Our commitment to excellence is even present in the sourcing of our shop tools and CNC Machines. Our shop is entirely equipped with Haas CNC Machines, locally manufactured right here in California.
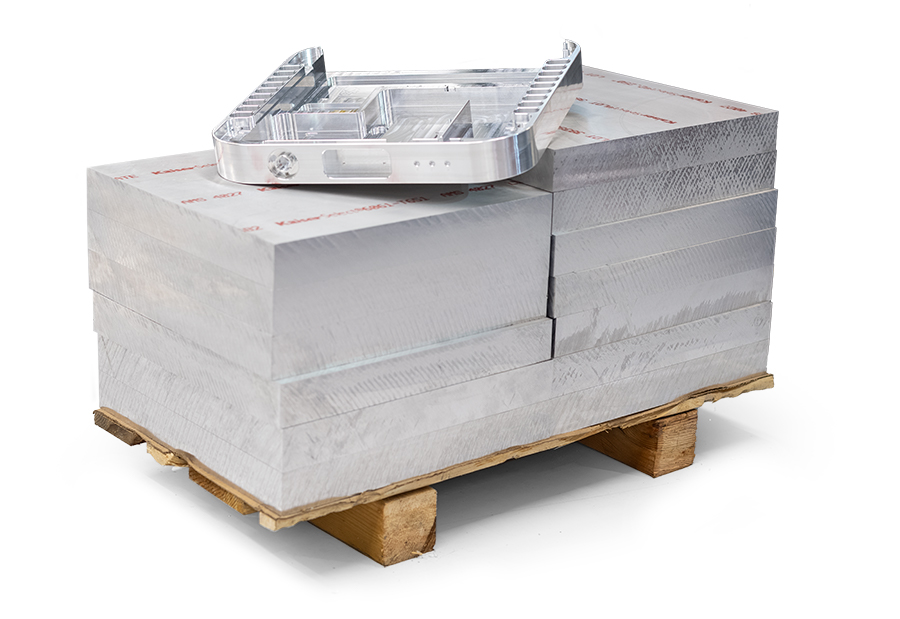
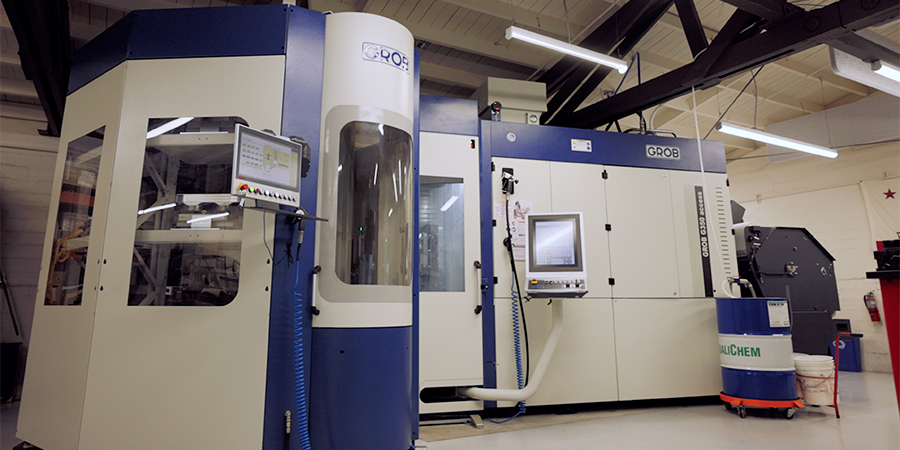
Step 4 – Machining
CNC Machining is the backbone of small business agile manufacturing. Larger scale productions usually incorporate parts made from metal castings, stamped metal, and plastic mold injected parts. Those processes, while producing less expensive parts, are less flexible and usually produce lower quality. Our in-house subtractive processes–which remove material from raw stock–allow us to produce high quality parts in smaller quantities, update and refine designs often, and constantly improve every detail. Our workflow prioritizes machined aluminum, but we also manufacture components from stainless steel, brass, Delrin, and copper. In order to precisely shape each part, we can choose the optimal cutting machine for its creation: a 5-Axis Mill , 3-Axis Mill, or a Lathe (Machining Center).
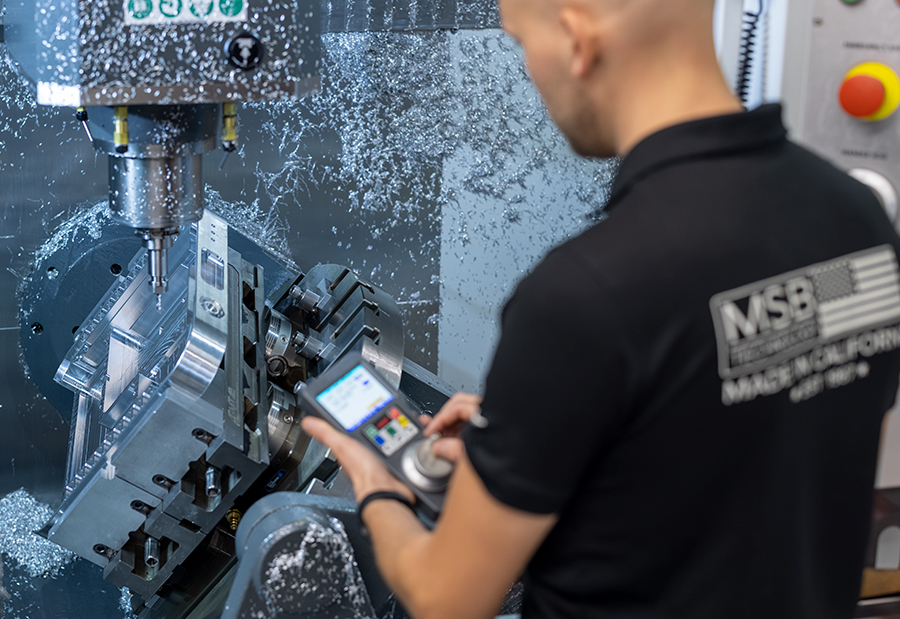
5-Axis Vertical Milling
The most exciting and productive machines we have are our 5-Axis Vertical Spindle Mills. 5-Axis refers to the five different ways the material can be automatically positioned by the machine for cutting. Our 5-Axis Mills is precise, able to carve smooth, complex curves and multiple sides of our chassis’ with minimal operator involvement. The mill is also sophisticated: it can machine the inside features before rotating the chassis to machine its faceplate and jackpanel. This form of automation increases quality, efficiency, and reliability.
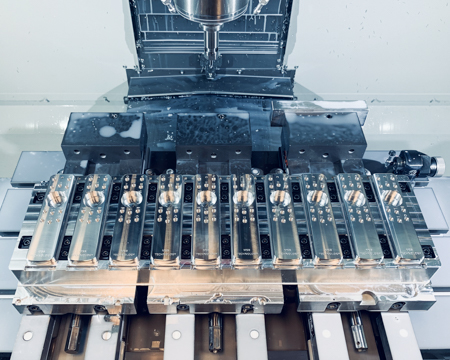
3-Axis Vertical Milling
With only three axis’ available, these workhorse milling machines manufacture simpler–but no less important–designs. In a manner of hours, it can produce an array of flat core plates, modules, brackets, base metal, and heatsinks. To increase productivity, we machine an array of parallel parts, reducing operator setups and boosting output.
Lathe Machining Center
Lathes are different from Vertical Mills in one big way: instead of spinning a cutting tool, they spin the part itself. Spinning the part allows for super smooth finishes on round products like buttons, knobs, screws, and feet. Our Lathe has two spindles to allow the complete machining of an entire component in one operation. Simply load a bar of stainless steel, press go, and in an hour, you’ll have over fifty product buttons produced without operator input.
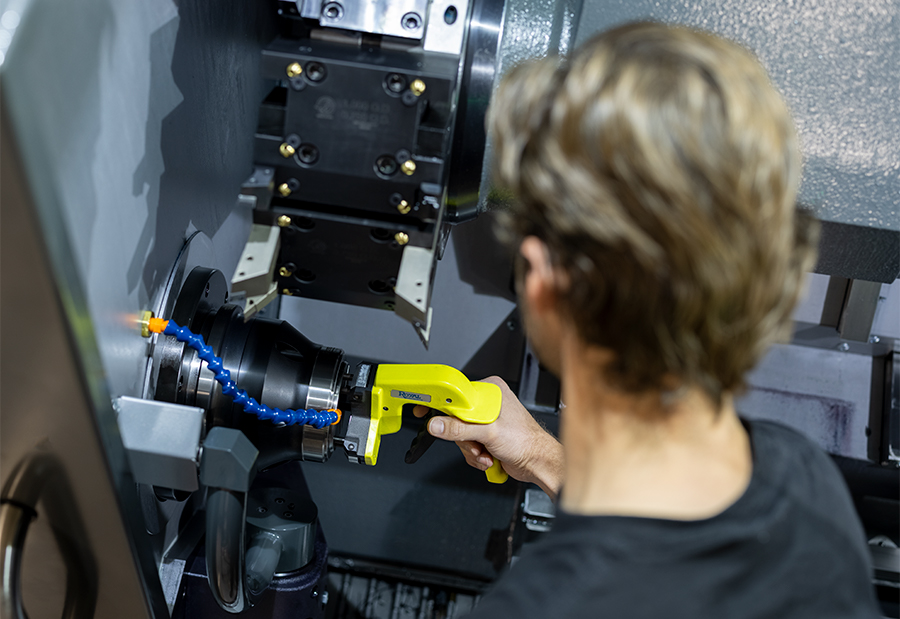
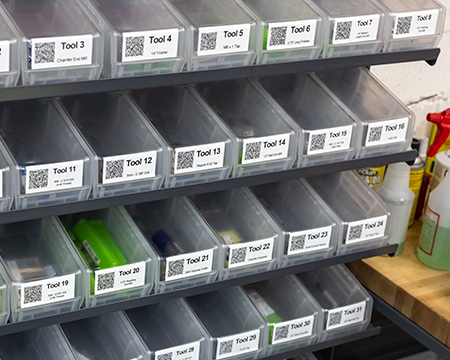
Lean Manufacturing
None of this would work without meticulous shop organization. Repeatable and consistent processes are critical to produce reliable, consistent products. Clean floors, clear labels, and precisely made parts are key components of our manufacturing methodology. We implement lean production principles to simplify part setup and verifications. Daily cleaning keeps our shop and equipment looking and performing its best.
Tooling
Curating a flexible yet powerful tooling library is vital for process reliability and product finishes. Tooling performance often comes down to rigidity and concentricity of the tool and tool holder. Traditional tooling, where you have a mechanical stack up with a tightening nut and collet result in less than ideal runout. This causes the end mill to cut on one tooth more than the others, aging quickly and needing to be replaced. Using a Haimer Heat Shrink system, the tool holder is heated up by a magnetic induction coil causing it to expand just enough to fit the endmill inside. As it cools, the tool holder shrinks back to its original size and grips the tool. The result is a strong connection that is near perfectly mated. This also reduces setup times, allowing us to have a more agile workflow.
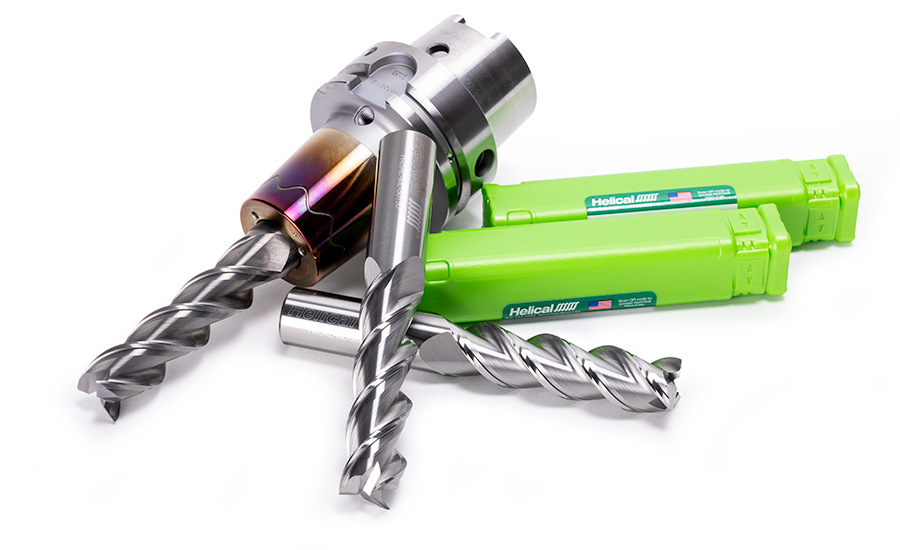
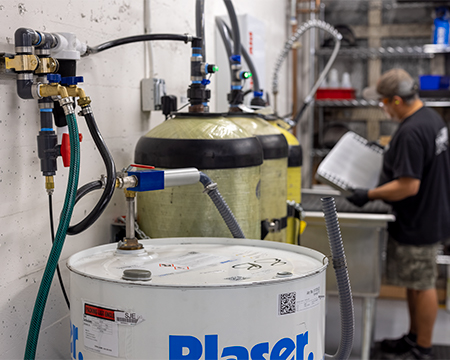
Coolant
Part finishes, part accuracy and tool life would be impossible without quality coolant. Coolant provides lubrication for the tooling edge, making the material easier to cut. Secondly, coolant removes metal chips from the cutting area, preventing repeat machine cuts. Finally, it keeps the tooling and workpiece cool and stable. We have installed a DI (Deionized) water system to tightly control the chemical balance of our coolant for optimal performance.
Metal Recycling
We prioritize machining aluminum, because it’s infinitely recyclable while being light, machinable, and robust. Nearly 75% of all aluminum ever produced is still in use today. We go above and beyond to sort and recycle all of our used metals in the manufacturing stream.
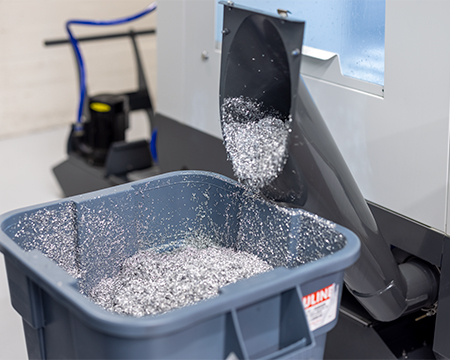
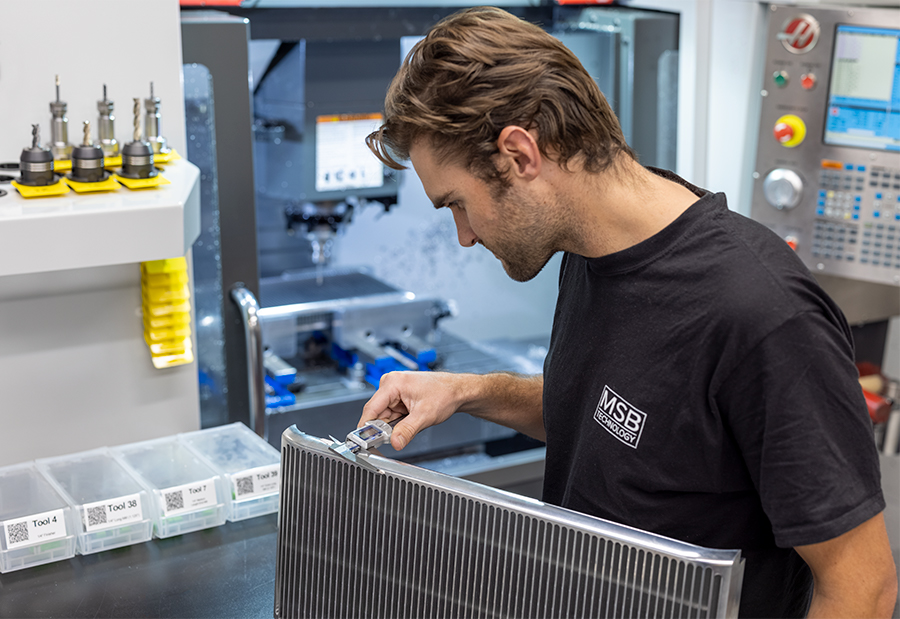
Step 5 – Inspection
Every machine shop requires strict attention to product inspection and tooling tolerances. Routine maintenance is performed on all of CNC machines and tooling, including measurement calibration. With integrated tooling and workpiece probe measurements, we can ensure repeated quality and accurate parts.
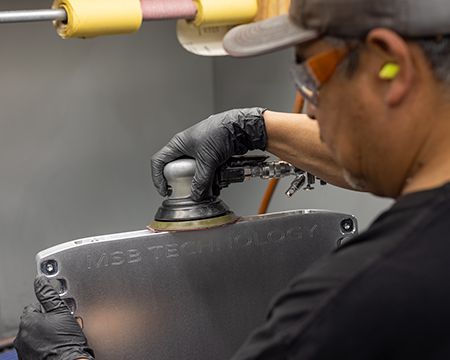
Step 6 – Hand Finished
Even with repeatable and stunning machine finishes, product aesthetic quality is a priority. Each of our product chassis are meticulously hand finished and inspected by skilled craftspeople. Our care and attention is present in each step of production; our hand finishes are no different. From there, we send hand-finished products to our local anodizing partner for the final finish. Anodizing results in a 100% recyclable product that lacks the chemical off-gassing filling your home that paint finishes produce. The beauty and feel of our anodized finishes are just one more small detail that adds to the MSB experience.