Our Production Process
Experience the final stages of our production process as our craftspeople meticulously assemble electronics within casework.

The Foundation: Inventory
Inventory control is the backbone of all manufacturing. While we’ve spent years improving and developing our inventory systems, today we rely on the lean manufacturing discipline known as Kanban. When any part or product is depleted to a set reserve, there’s an alert to begin reordering or manufacturing. A quick scan of the QR code sets this process into motion. This may sound simple, but can easily become complex when dealing with thousands of parts and vastly different lead times. We put the extra effort in to help maintain a consistent workflow with reliable delivery times.
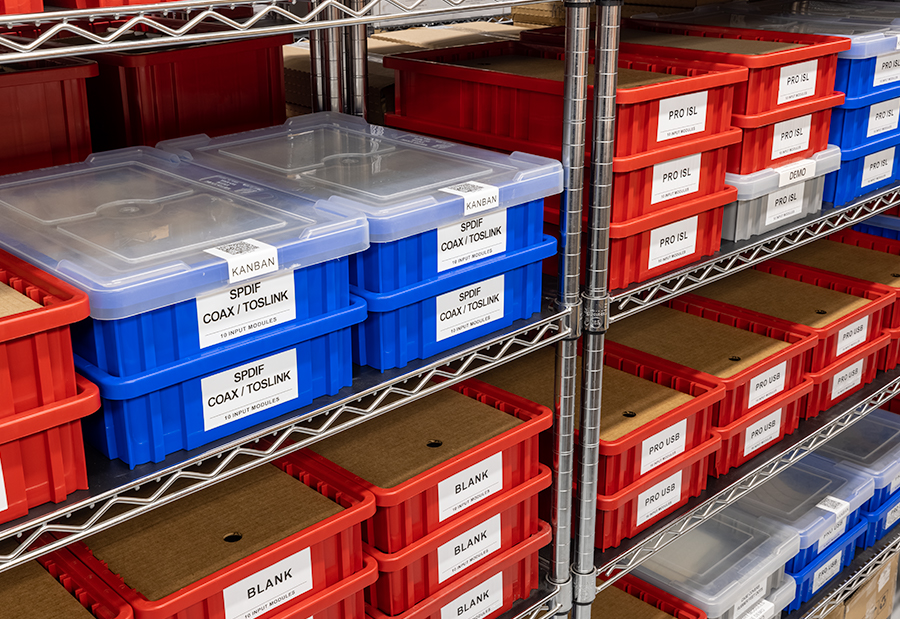
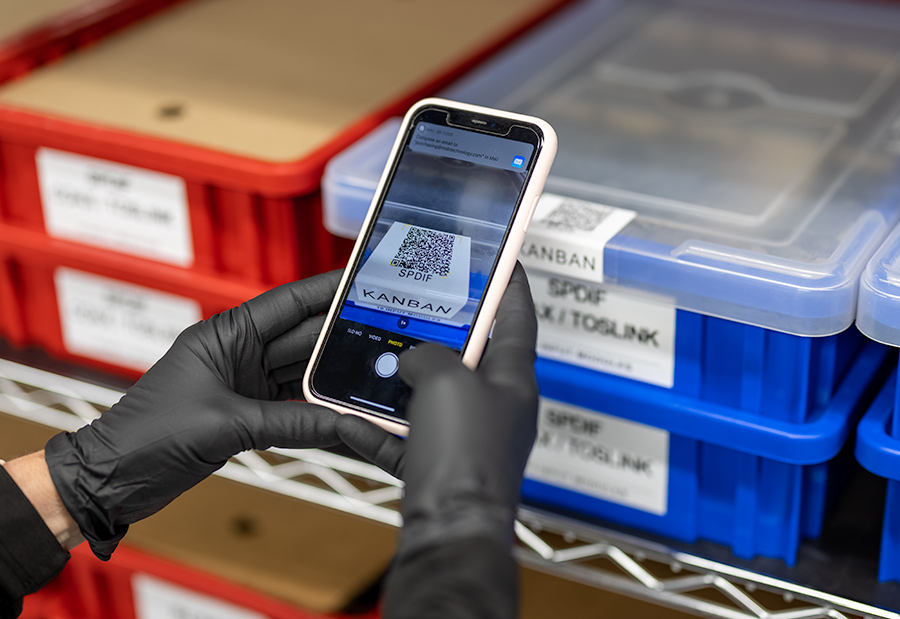
Reliability: Sub-Assemblies
One of our greatest strengths is the modular design found in every product we produce. While the benefits may seem obvious, some are less so. In a production environment, pretesting modules guarantee a single build from start to finish. This reduces the amount of handling, shortens lead times, and results in the highest performing product. Every DAC module is measured in advance and installed as a hand-selected matching set. Some long-term benefits include easy to install upgrades and repairs. When dealing with digital technology, flexibility is needed to quickly adapt to new audio formats or connections. Depending on the system, existing modules can be swapped out to add a network renderer or extra toslink connections. This is the only way to deliver a fully tailored solution.
Optimization: Rapid Tooling
We pride ourselves on creating effective production processes for the most reliable assembly and long term performance. With our in-house machine shop, custom machined tools are made for bending part leads, inserting bearings, and setting alignments. Recycled cardboard is laser-cut into custom product packaging, while 3D printed dividers are shaped to perfectly hold and protect parts in our inventory. Whatever the need, we’re easily able to craft creative solutions for a smooth workflow.
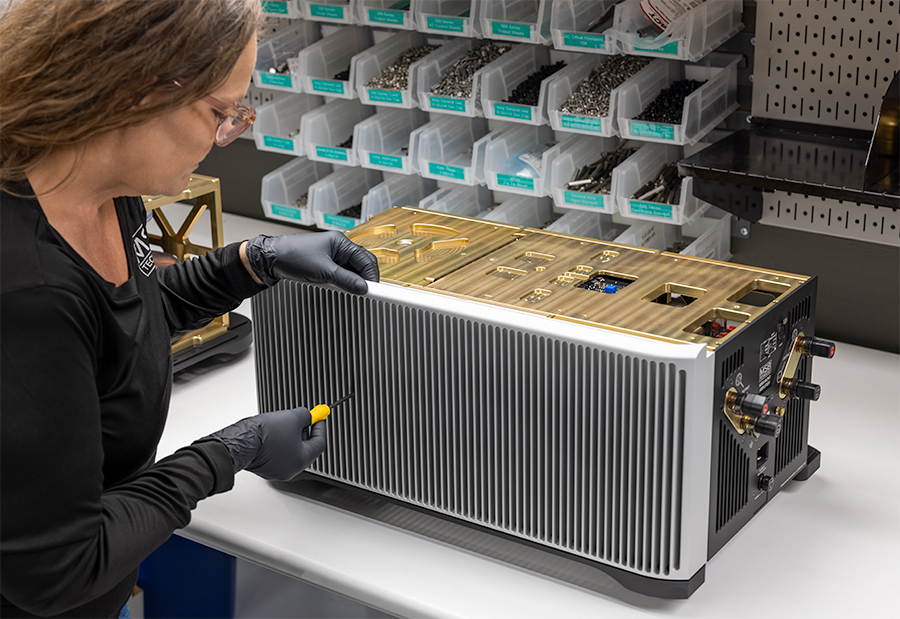
Lean Manufacturing: Build Stations
Individual workstations are set up for each type of product we manufacture. These are highly focused areas equipped with the specific hardware and parts needed for a dedicated product. Our hand-built product is entirely built to order. After kitting the major components (chassis and sub-assemblies) one of our production technicians completes a build from start to finish at one station. This reduces distractions, time wasted moving product, and eliminates access to the wrong hardware or tooling.
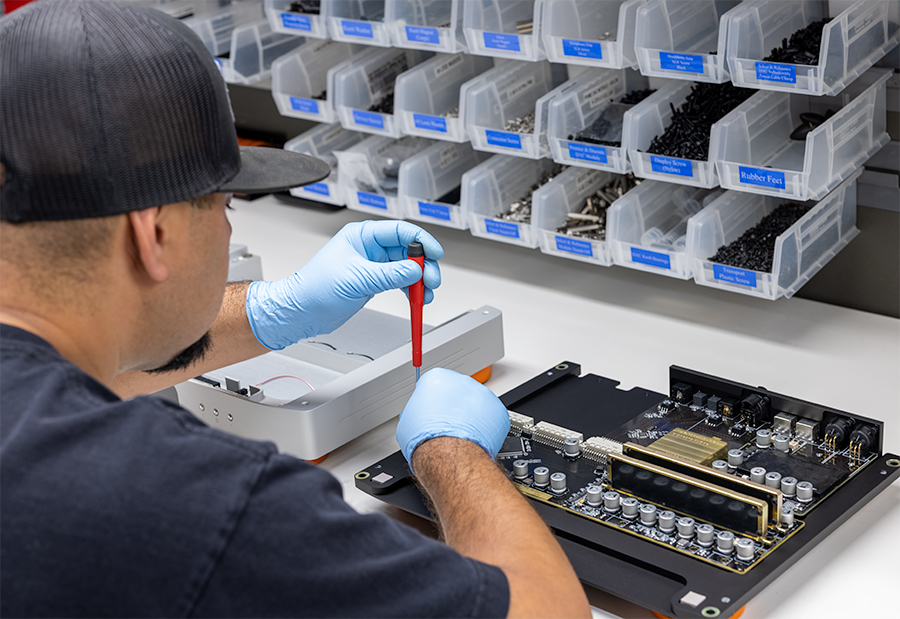
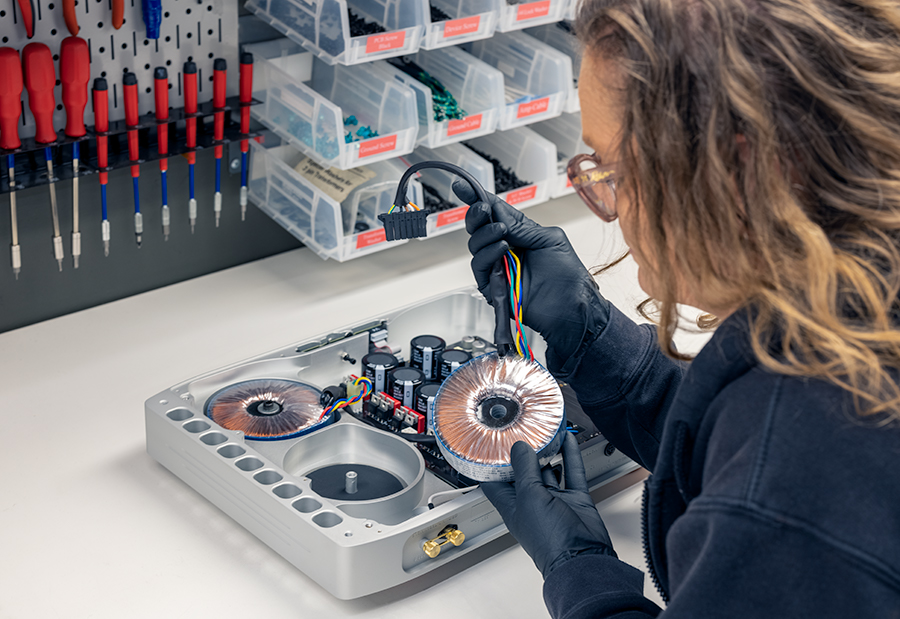

Measurement: Audio Precision
Audio Precision systems are the gold standard for measuring audio equipment. Two in-house Audio Precision systems are used throughout every stage of development and production. Each internal module and board is individually tested and measured before final assembly. Once the unit is completed and has passed the functionality testing, it’s measured as a complete system. Our highly customized and automated testing can run hundreds of different tests and measurements, checking everything from the word sync output to every detail of the analog outputs. Our engineers have set strict standards to ensure that every unit is working perfectly. . Nothing ships that does not surpass our expectations.
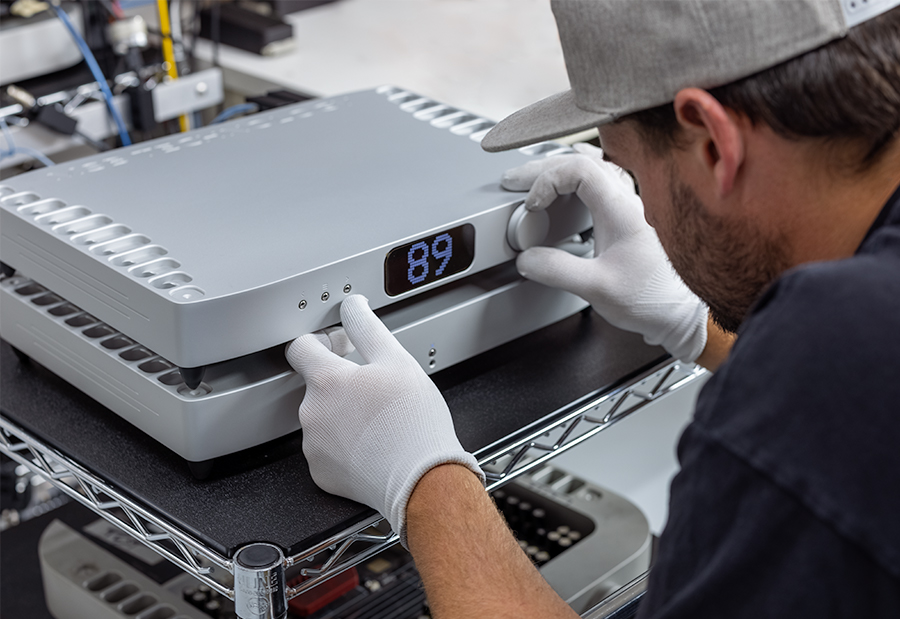
Performance: Functional Testing
The Audio Precision system is only able to test electrical performance. Each unit still requires a technician to perform a functional test on all of the mechanical components. This entails clicking every button, checking the IR receiver, and spinning volume knobs. This is also where each DAC is programmed with a unique serial number and distributor name. This allows us to keep track of units in the field and provide support when needed.
Shipping: cleaned, inspected, and boxed
At the final stage of production, we have a complete system gathered, tested, cleaned and ready to be inspected. Extra options and modules are gathered as well. This will then be compared against the order invoice to ensure options and custom build instructions have been met. Our shipping manager will meticulously clean and inspect the entire system in preparation for an owner inspection. Jonathan or Daniel will do a final white glove inspection of the system, accessories and packaging. After boxing, labels are applied and then the order is on its way.
Quality Control: Owner Inspection
In the earlier days of our company, Jonathan and Daniel worked on every product that shipped out the door. As the company grew, they insisted on staying involved and connected with every order. Either Jonathan or Daniel perform a white glove inspection of every unit. Their initials can be found signed on the packaging of every DAC shipped. It is a stamp of quality and confidence in our products.
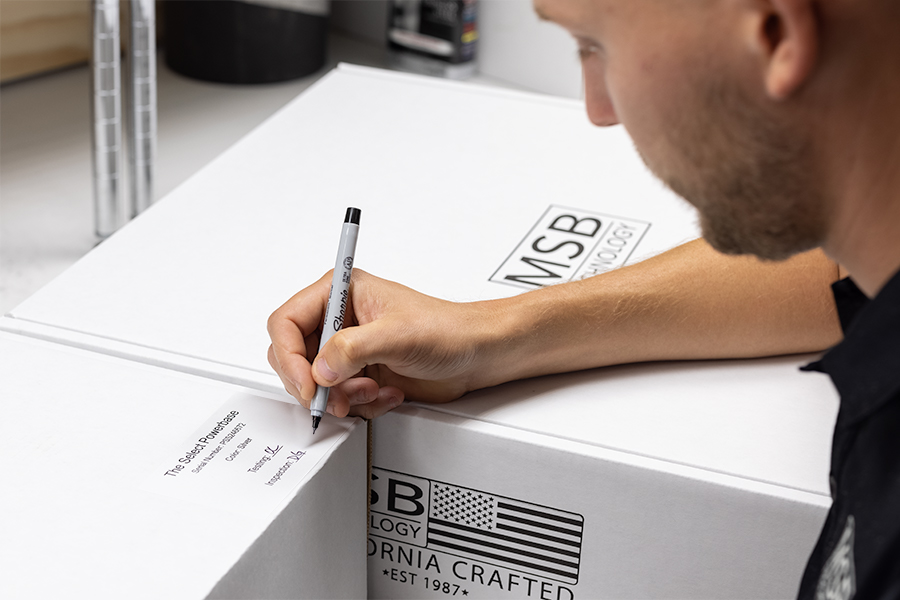